Особенности проектирования систем аспирации дозировочно-смесительных линий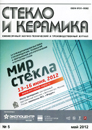 С появлением широкого типоразмерного ряда компактных рукавных фильтров, оснащенных встроенными вентиляторами и блоками автоматического управления регенерацией фильтровальных элементов, процесс проектирования и построения высокоэффективных систем аспирации дозировочно-смесительных и транспортно-технологических линий составных цехов существенно упростился. Взамен централизованных систем аспирации, состоящих из одного-двух мощных вентиляторов, нескольких ступеней одиночных или батарейных циклонов, а также громоздкого фильтра и разветвленной сети воздуховодов с регулируемыми и нерегулируемыми дисковыми заслонками и ножевыми задвижками, стали использоваться локальные рукавные фильтры небольшого размера, устанавливаемые в местах пересыпки и наибольшего пыления сыпучих материалов. Такими местами в дозировочно-смесительных линиях (ДСЛ) являются сборочный конвейер, на который в процессе дозирования выгружаются основные компоненты стекольной шихты, и смесители, в которых эти материалы, а также красители и обесцвечиватели стекломассы, чаще подаваемые в смесители напрямую, перемешиваются и увлажняются в соответствии с заданной циклограммой. На линии дозирования обычно устанавливают один рукавный фильтр, который размещают ближе к смесителю и иногда монтируют непосредственно на укрытии приводной станции сборочного конвейера. Реже, если количество дозаторов превышает 5-6, а сборочный конвейер имеет длину более 30 м (горизонтальная компоновка составного цеха), используют дополнительный пылеулавливающий агрегат, который смещают к центру или хвостовой части конвейера. В некоторых случаях рукавный фильтр, размещенный в головной части сборочного конвейера, соединяется с помощью отдельного воздуховода со смесителем и осуществляет одновременное обеспыливание процессов дозирования и смешивания, создавая необходимое разрежение не только внутри укрытия рабочего пространства конвейера, но и в смесителе шихты. Однако подобная система пылеулавливания используется не всегда и в большей степени определяется не технологической целесообразностью, а экономией средств на приобретение и монтаж дорогостоящего аспирационного оборудования. Поскольку для удаления избыточного объема запыленного воздуха, вытесняемого из смесителя загружаемыми материалами, требуются фильтры с относительно высокой производительностью и большой площадью фильтрации рукавных элементов (см. таблицу), а при увлажнении шихты водой и возможном дополнительном подогреве паром про¬исходит быстрое залипание пор фильтровальной ткани, целесообразна установка автономных фильтров или других аспирационных устройств, соединенных только со смесителями и не связанных с другим технологическим оборудованием ДСЛ. Кроме того, аспирационные устройства должны иметь фильтровальные элементы из специальной ткани с масловлагозащитным покрытием, снижающим ее быстрое намокание и загрязнение. Таблица. Технические характеристики фильтров систем аспирации смесителей | Характеристики фильтра | Объем смесителя, л | Тип фильтра* | Производительность, м3/ч | Площадь фильтрации, м2 | Потребляемая мощность вентилятора, кВт | Габаритные размеры, м | Масса, кг | 750 | FC2J07 | 500 | 7 | 0.75 | d 600; H=1.48 | 85 | 1500 | FC2J13 | 1000 | 13 | 1.1 | d 600; H=1.9 | 126 | 2250 | FC3J20 | 1500 | 20 | 1.5 | d 800; H=1.84 | 164 | 3000 | FC4J25 | 2000 | 25 | 2.2 | d 1000; H=1.67 | 219 | 4500 | FC4J39 | 2500 | 39 | 2.2 | d 1000; H=1.92 | 243 |
* Цилиндрические воздушные фильтры серии WAMECOконцерна WAMGROUP(Италия). Типовая схема стыковки рукавного фильтра со смесителем шихты (рис. 1) предусматривает, как правило, нижнюю подачу очищаемого воздуха в фильтр 1 и нижний сброс регенерируемой пыли в смеситель 2 через один и тот же соединительный воздуховод 3, снабженный одной или двумя отсеченными заслонками 4 с пневмоприводом. Наличие даже одной заслонки позволяет эффективно отсекать работающий фильтр от смесителя после окончания сухого перемешивания компонентов стекольной шихты и тем самым защищать фильтровальную ткань от интенсивных испарений подогретой воды во время операции увлажнения смеси.
А при использовании двух последовательно установленных дисковых заслонок, образующих шлюзовый затвор, негативное влияние влажного и запыленного воздуха на фильтр и верхнюю заслонку затвора минимизируется.
Если же отсечная заслонка вообще отсутствует в технологической схеме ДСЛ, а шихта производится в режиме сухого смешивания (этот режим наиболее эффективен в смесителях ТЕКА и EIRICH), то для снижения отрицательного воздействия влаги на поверхность фильтровальных элементов требуется автоматическое отключение вентилятора фильтра на все время от начала увлажнения шихты до окончания выгрузки ее в приемную воронку. Но это лишь частично решает указанную проблему и не исключает необходимости более тщательного профилактического ухода за работой аспирационного оборудования, так как нижняя часть фильтров, находящихся в зоне сброса регенерируемой пыли, все равно покрывается капельной влагой и постепенно обрастает коркой из соды, доломита и других наиболее пылящих компонентов стекольной шихты. 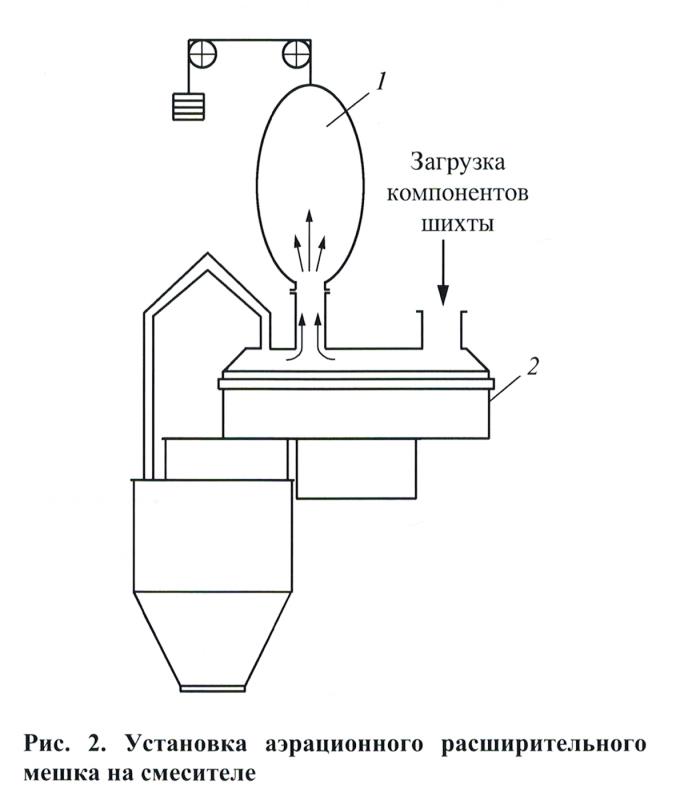
Особенно быстро подобные наросты, препятствующие нормальной работе фильтровальных элементов, образуются при использовании традиционной технологии смешивания, при которой сначала увлажняется песок в смесителе, а затем загружаются остальные материалы смеси. В этом случае установка отсечных дисковых заслонок на аспирационном патрубке теряет всякий смысл, так как избыток воздуха, вытесняемого из смесителя при загрузке кварцевого песка, остается сухим только в первый момент времени перед началом распыления воды, увлажняющей шихту. Естественно, что в подобном режиме обеспыливания влажного воздуха фильтры засоряются за 5-7 дней эксплуатации и без тщательной дополнительной очистки (автоматическая регенерация уже не помогает) и стирки рукавов перестают функционировать. Интересно, что в отечественной и зарубежной практике приготовления стекольной шихты процесс обеспыливания воздуха, вытесняемого из смесителя при дозированной загрузке и перемешивании сырьевых материалов, осуществляется и другими, более дешевыми по сравнению с рукавными фильтрами, аспирационными устройствами и способами. Простейшим таким устройством (рис. 2) является аэрационный мешок 1 из пыленепроницаемой ткани, который выполняет функцию расширителя и имеет объем, сопоставимый с объемом загружаемого в смеситель 2 материала. Недостатком этого мешка, часто поставляемого в качестве недорогой опции со многими марками зарубежных смесителей, является его схлопывание при выгрузке шихты после ее перемешивания, в результате чего часть сконцентрированного в мешке запыленного воздуха выбрасывается в приводную станцию сборочного конвейера, образуя нежелательное пыление. Выброс частично локализуется, если перекидную заслонку рукавного переключателя, расположенного между сборочным конвейером и смесителем, перед выгрузкой шихты перевести в положение, соответствующее загрузке материала в другой смеситель, что возможно лишь при соответствующей компоновке ДСЛ и работе весовой линии на два смесителя. К следующим отрицательным моментам в эксплуатации аспирационных систем, построенных на основе аэрационных мешков-расширителей, можно отнести слабое проветривание внутреннего объема и постоянное налипание влажной шихты на стенки и вращающиеся элементы смесителя, регулярную очистку которого приходится проводить в конце каждой рабочей смены.
Эти же недостатки свойственны и другой конструкции расширителя объема воздуха, выполненного из фильтровальной ткани, натянутой на легкий металлический каркас и образующей своеобразный цилиндрический рукав с ограниченным объемом, равным 0,5 - 0,8 м3. Ткань рукава в отличие от аэрационного мешка не схлопывается и пропускает через себя отфильтрованный воздух, но, как и все фильтры, также быстро загрязняется, хотя замену и стирку ее производят значительно реже - один раз в два месяца. Лучшей аэрации внутреннего объема смесителя в процессе приготовления стекольной шихты достигают с помощью простой вытяжной трубы (рис. 3) диаметром 200-300 мм, осуществляющей факельный выброс избытка влажного воздуха в атмосферу на высоту 12-16 м. Иногда при необходимости значительного увеличения объема трубы, например при объеме смесителя более 1500 л и при вертикальной компоновке составного цеха, в которой большие порции материала быстро загружаются в смеситель, в разрыв трубы дополнительно устанавливают расширительную емкость или циклон, способствующие также осаждению пыли. Удаление избыточного воздуха из этой емкости и обеспечение требуемого разрежения в системе проводят либо за счет естественной тяги (рис. 4, а), либо с помощью вентилятора (рис. 4, б), скорость вращения двигателя которого может изменяться с помощью частотного регулятора. Правда, при использовании естественной или принудительной тяги вытяжной трубы есть опасения, что часть легких фракций шихты может улетучиваться, поэтому на некоторых заводах выход расширительной емкости не соединяют с атмосферой, а перекрывают фильтровальным колпаком. 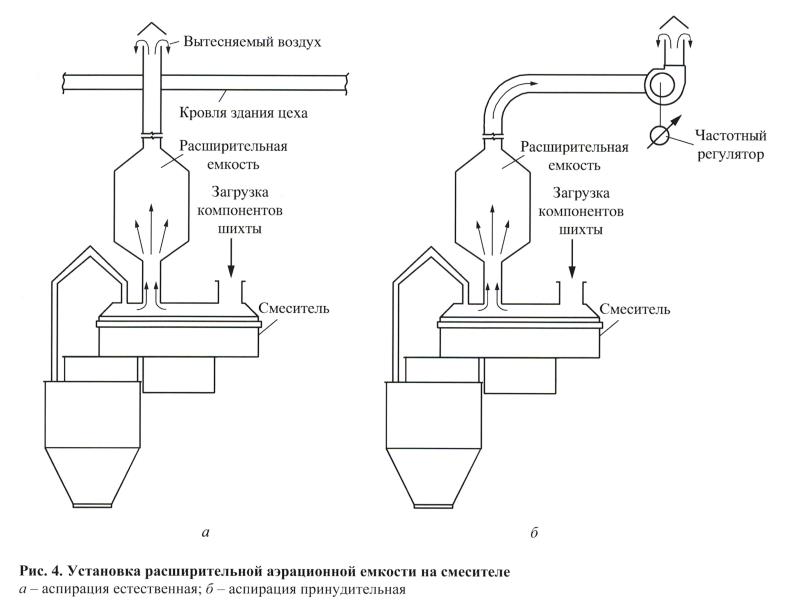
Все эти технические решения при кажущейся простоте имеют определенные недостатки, поэтому наилучшего результата при проектировании эффективных систем аспирации достигают не только простым подбором той или иной модели фильтра, циклона или другого устройства, но и комплексным подходом к вопросам строительной и технологической компоновок составного цеха, выбора основного и вспомогательного оборудования ДСЛ и разработки оптимальных алгоритмов управления. 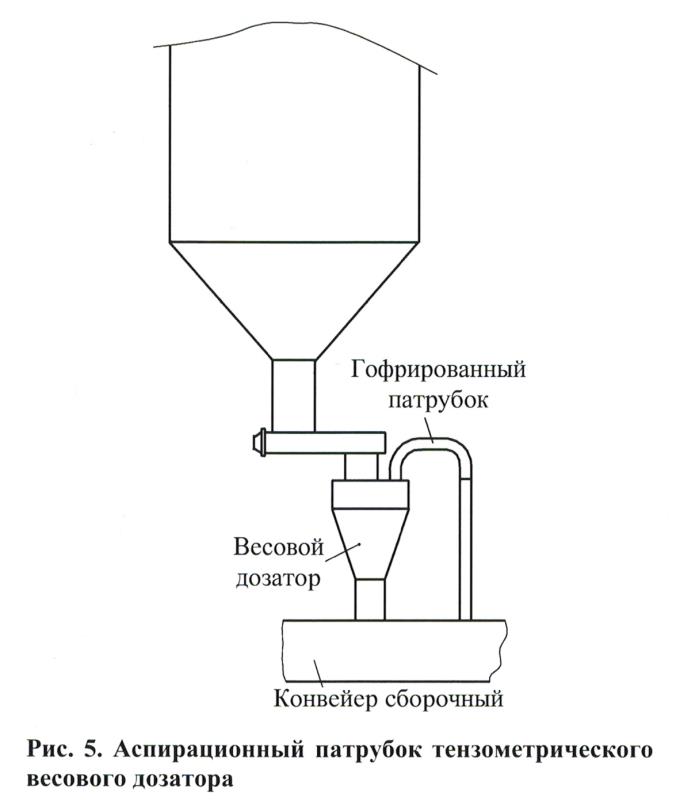 В процессе проектирования систем аспирации ДСЛ решают и другие задачи, связанные не только с операциями смешивания и увлажнения сырьевых материалов, но и с их дозированием, так как точная работа тензометрических весовых дозаторов (особенно это касается дозирования малых компонентов стекольной шихты) напрямую зависит от величины разрежения, создаваемого аспирационным оборудованием в смесителе и внутреннем объеме укрытия сборочного конвейера. Чтобы исключить это нежелательное влияние на точность взвешивания сырьевых материалов (200 - 300 г), вызванное разностью между атмосферным давлением и давлением внутри аспирируемого оборудования, устанавливают гофрированные патрубки (рис. 5), которые соединяют крышки тензометрических дозаторов с крышками сборочных конвейеров и выполняют две основные функции: выравнивают давление между агрегатами и стравливают воздух из весовых дозаторов во время заполнения их материалом. За состоянием гофрированных патрубков необходимо постоянно следить, так как они постепенно забиваются пылью, становятся менее гибкими и тем самым вносят определенные погрешности в работу весоизмерительных систем. Поэтому вместо гофрированных пластиковых патрубков иногда используют другие узлы (рис. 6), состоящие из двух металлических труб 1, 2, связанных между собой с помощью воздушно-регулируемого затвора 3, имеющего форму перевернутой конусообразной воронки 4. С помощью подобных устройств обычно выравнивают давление и в приемных бункерах шихты, выгружаемой из смесителей, что особенно важно, если эти бункера устанавливают на весовые датчики, контролирующие полноту разгрузки смесителя и предотвращающие попадание второго замеса в бункер.
Дополнительные технические мероприятия, улучшающие работу весового оборудования и повышающие точность взвешивания сырьевых материалов, включают в себя монтаж отсечных заслонок и шлюзовых затворов в разгрузочных течках дозировочных и дозировочно-смесительных комплексов малых компонентов стекольной шихты, к которым относятся сульфат, уголь, красители, премиксы селена и кобальта и другие обесцвечиватели стекломассы. Шлюзовые затворы (рис. 7), состоящие из двух дисковых заслонок 1, 2, также как и при работе их в комплексе с рукавным фильтром, защищают механизм поворотной чаши 3 дозатора 4 микродобавок от воздействия влажного и запыленного воздуха и предотвращают возможные колебания чувствительной весоизмерительной системы дозатора малых компонентов, вызываемые изменением давления воздуха внутри смесителя 5. Подобную проблему можно устранить и другим способом, если отдозированные микродобавки и их премиксы загружать не напрямую в смеситель, а предварительно подавать их в дозатор сульфата или другого малого компонента шихты, вводимого в небольших количествах (рис. 8), из которого они вместе выгружаются на сборочный конвейер. Причем разгрузочная течка 1 этого дозатора 2 должна обязательно содержать отсечную заслонку 3, исключающую влияние аспирационной системы на точность взвешивания. Игнорирование этого требования для дозаторов малых порций может привести к недопустимым погрешностям дозирования (в несколько сотен грамм) вследствие воздействия силы тяги, что приводит к ложным срабатываниям системы управления, фиксирующей либо «выброс тары дозатора», либо утечку сырья из отсечной заслонки питателя загрузки, либо досрочное заполнение бункера весов. Дозаторы же песка, соды, доломита и других материалов, не относящихся к малым добавкам, менее чувствительны к колебаниям давления внутри сборочного конвейера, поэтому при проектировании в их конструкцию не закладываются дополнительные затворы. 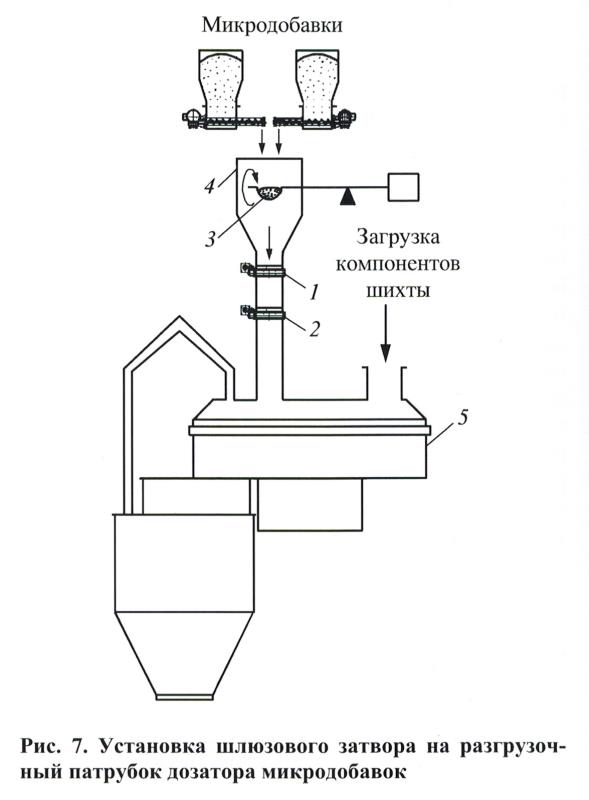 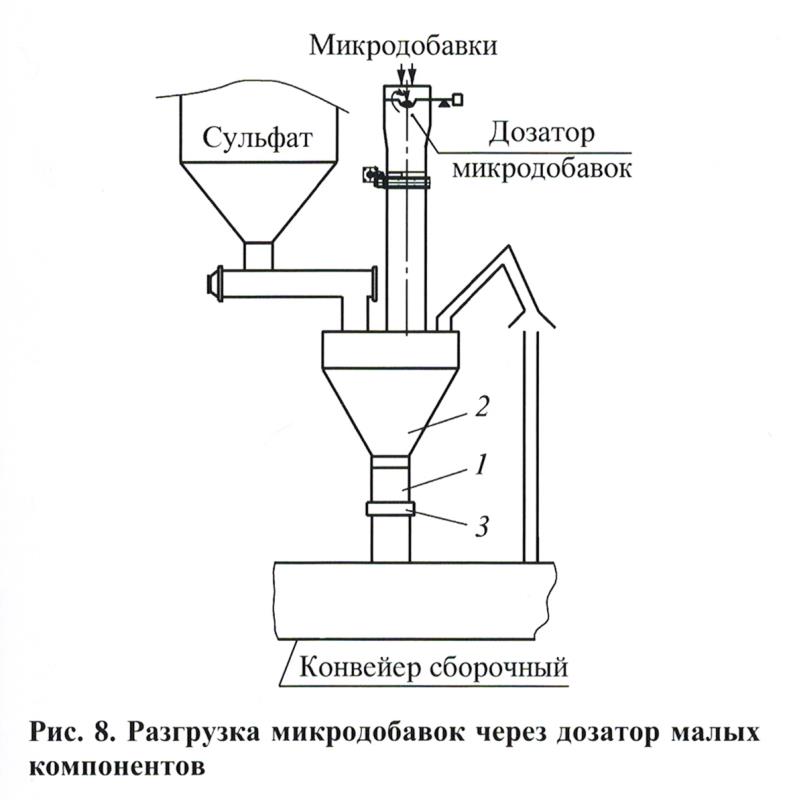
Проектирование систем аспирации ДСЛ, построенных на основе передвижных дозировочных комплексов [2], имеет другие особенности, обусловленные горизонтальной компоновкой и протяженностью подобных весовых линий, а также большим количеством позиций загрузки и выгрузки материалов. Как правило, эти системы централизованные и оснащаются стационарно установленным пылеулавливающим оборудованием и разветвленной сетью воздуховодов и патрубков с щелевыми отсосами и регулируемыми задвижками. При этом воздуховоды, имеющие длинные горизонтальные участки, постоянно забиваются пылью, уловленные циклонами и фильтрами материалы не возвращаются в технологический процесс, а подлежат утилизации. Более эффективной работой отличаются мобильные системы аспирации [3] весовых тележек, в которых герметизирующие стыковочные узлы, исключающие пыление дозируемого материала при его загрузке в весовой бункер и последующей разгрузке в смеситель, а также рукавный фильтр, ресивер сжатого воздуха и пневмоприводы стыковочных механизмов и дисковых поворотных заслонок установлены непосредственно на тележке, что не только значительно сокращает общее количество приводов системы, но и существенно снижает потери компонентов стекольной шихты. Таким образом, разработка и внедрение эффективных решений при проектировании современных систем аспирации ДСЛ позволяет повысить качество приготавливаемой шихты и различных многокомпонентных смесей и улучшить санитарное состояние составных цехов и дозировочно-смесительных отделений. Канд. техн. наук В.В. Ефременков (stromizmeritel@rambler.ru) Группа компаний "Стромизмеритель" (Россия, г. Нижний Новгород) Список литературы 1. Ощекина Е. Ю., Королева С. В. Проектирование систем аспирации в составных цехах стекольных заводов // Стекло и керамика. 2005. №4. С. 38-41. 2. Ефременков В. В. Особенности использования транспортных и электровесовых тележек в производстве стекольной шихты // Стеклянная тара. 2009. № 11. С. 12 - 14. 3. Ефременков В. В., Ощекина Е. Ю. Проектирование систем аспирации составных цехов // Стеклянная тара. 2009. № 6. С. 22-24. |